Highest purity standards for coating systems
Ultra Pure Water (UPW) is crucial for coating equipment because it meets the highest purity standards and is free of contaminants such as inorganic particles, ionic materials, microorganisms and organic compounds. Here are some key aspects of UPW in coating equipment:
Precision and passion - water quality Made in Germany by Artas ultrapure water systems
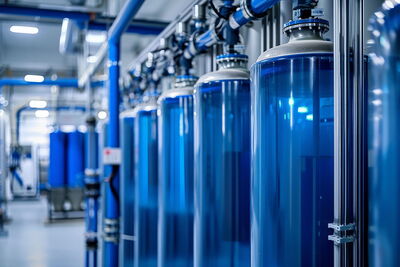
High electrical resistivity: UPW has an electrical resistivity of 18.3 MegOhm-cm, indicating the absence of dissolved ions.
No contaminants: UPW contains only water, hydrogen ions, and hydroxide ions, which is essential for processes that require high purity1
Material selection: The materials used must have smooth, non-porous surfaces and must not contain biodegradable substances that could serve as sources of nutrients
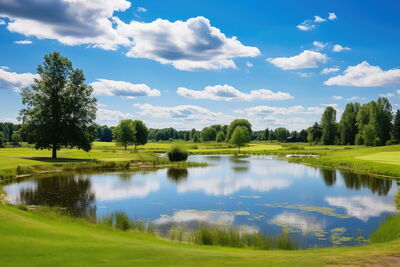
System design: Speeds, pressures and flows must be precisely controlled to ensure the purity of the water delivered. Care must also be taken to eliminate "dead legs" (non-flowing areas) within the equipment and pipe system.
In coating equipment, UPW is used to clean and rinse surfaces prior to coating to ensure that no residue or particles affect the quality of the coating. The use of UPW helps to improve the consistency and reliability of coating processes and increase the performance of the final products.
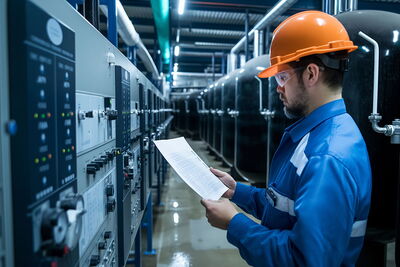
In the painting industry, typical ultrapure water process units are of great importance to ensure high quality of painting. Here are some of the key components:
Pre-treatment: Removes greases, oils and other contaminants from the surface of the parts to be painted.
Deionization: Removes ions from the water to prevent the formation of deposits and corrosion during the painting process.
Reverse osmosis: Separates dissolved solids and microorganisms from the water to achieve high purity.
Microfiltration: Removes the finest particles that could affect the quality of the paintwork.
UV sterilization: Disinfects the water by killing bacteria and viruses to prevent microbiological contamination